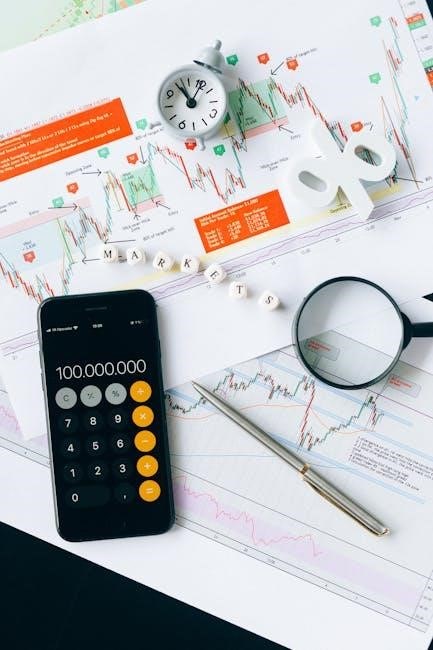
helicoil tap drill chart pdf
Helicoil Tap Drill Chart PDF: A Comprehensive Guide
This guide serves as a comprehensive resource for understanding and utilizing Helicoil tap drill charts, essential for effective thread repair and reinforcement․ Accessing a PDF version allows for convenient offline access to crucial sizing information, vital for selecting the correct drill and tap sizes․
Helicoil inserts, also known as screw thread inserts, are precision-formed coils of stainless steel wire, characterized by a diamond-shaped cross-section․ These inserts are designed to provide strong, durable threads in softer materials like aluminum, magnesium, and even some plastics, offering a robust solution where original threads may be weak or damaged․ Since their inception in 1938, Helicoil inserts have become a highly regarded and readily recognized product in the industry, revolutionizing fastening and assembly technologies․
The primary function of a Helicoil insert is to create a more resilient and longer-lasting thread, capable of withstanding greater loads and repeated use․ They are particularly useful in applications where frequent assembly and disassembly are required, preventing thread wear and tear․ By distributing the load over a larger area, Helicoils minimize the risk of thread stripping, ensuring a secure and reliable connection․
Furthermore, Helicoil inserts can be used to repair stripped or damaged threads, restoring the component to its original functionality without the need for costly replacements․ These inserts are available in various materials, including Nimonic 90, Nitronic 60, Titanium alloys, and Inconel X-750, catering to a wide range of specialized applications․
Understanding Helicoil Thread Repair Kits
Helicoil thread repair kits are comprehensive sets designed for restoring damaged or stripped threads in various materials․ These kits typically include several essential components: Helicoil inserts, a specialized Helicoil tap, an installation tool, and detailed instructions․ The Helicoil tap is specifically designed to create the correct thread size for accommodating the Helicoil insert․
The installation tool is used to insert the Helicoil into the newly tapped hole․ These kits provide a cost-effective and efficient solution for repairing damaged threads, eliminating the need for replacing entire components․ Metric and inch series kits are available to suit different thread standards․ The kits often include inserts of varying lengths (1D, 1․5D, 2D, etc․) to cater to different application requirements․
When using a Helicoil thread repair kit, it’s crucial to follow the instructions carefully to ensure proper installation and optimal performance․ The process typically involves drilling out the damaged thread, tapping the hole with the Helicoil tap, and then installing the insert using the provided tool․ These kits are widely used in automotive, aerospace, and general industrial applications, offering a reliable method for thread repair and reinforcement․
Benefits of Using Helicoil Inserts
Helicoil inserts offer numerous advantages in thread repair and reinforcement․ One primary benefit is their ability to restore damaged threads to their original strength, often exceeding the strength of the original thread․ This is particularly valuable in materials like aluminum, where threads are prone to stripping․
By using Helicoils, engineers can avoid costly component replacements, as the inserts provide a durable and reliable thread․ Helicoil inserts are made from stainless steel wire, offering excellent corrosion resistance and durability in harsh environments․ The inserts also help distribute load evenly across the thread engagement, reducing stress and improving the overall joint strength․
Another advantage is the ability to use the same size bolt or screw after the repair, maintaining the original design intent․ Helicoil inserts are relatively easy to install using the correct tools and techniques․ They are also available in various sizes and lengths, accommodating a wide range of applications․ Furthermore, using Helicoils can prevent thread seizure and galling, ensuring smooth assembly and disassembly․ Overall, Helicoil inserts provide a cost-effective, reliable, and efficient solution for thread repair and reinforcement, enhancing the performance and longevity of threaded connections․
Helicoil Drill Size Chart: Imperial (Inch) Series
The Imperial (Inch) series Helicoil drill size chart is an essential reference for selecting the correct drill size when preparing a hole for Helicoil insert installation․ This chart provides the necessary drill sizes for various Imperial thread sizes, ensuring a proper fit and optimal performance of the Helicoil insert․ The chart typically lists the nominal thread size, the corresponding tap drill size (usually expressed in fractions of an inch), and sometimes the STI (Screw Thread Insert) tap size․
Using the correct drill size is crucial because an undersized hole can make tapping difficult or impossible, while an oversized hole can compromise the holding power of the insert․ The chart helps users avoid these issues by providing precise drill size recommendations․
These charts are often available in PDF format for easy access and printing․ Many charts also include decimal equivalents of the fractional drill sizes, further simplifying the selection process․ Consulting the Imperial Helicoil drill size chart before starting any Helicoil installation is vital for achieving a successful and durable thread repair․ This ensures that the insert will properly engage with the parent material and provide the intended thread reinforcement․
Helicoil Drill Size Chart: Metric Series
The Metric Series Helicoil drill size chart is a vital tool for accurately preparing holes when installing metric Helicoil inserts․ This chart specifies the precise drill sizes needed for various metric thread sizes, ensuring a correct fit and optimal functionality․ The chart typically lists the metric thread size (e․g․, M6x1․0) alongside the corresponding drill size, usually expressed in millimeters․
Selecting the correct drill size is paramount․ A hole that’s too small will hinder tapping, while an oversized hole diminishes the insert’s grip․ These charts eliminate guesswork by offering exact drill size recommendations․
Metric Helicoil drill size charts are frequently available as PDFs for convenient access and printing․ They are indispensable for anyone working with metric threads and Helicoil inserts․ Consulting this chart before installation guarantees a successful thread repair, allowing the insert to properly engage and reinforce the material․ The chart is invaluable for maintaining the integrity and reliability of threaded connections in metric applications, preventing failures and extending the lifespan of components․
How to Read a Helicoil Tap Drill Chart
Understanding a Helicoil tap drill chart is crucial for successful thread repair․ Typically, the chart is organized into columns, with the first column listing the nominal thread size (e․g․, 1/4-20 or M6x1․0)․ The subsequent column indicates the recommended drill size for preparing the hole to accept the Helicoil tap․ This drill size is larger than the standard tap drill size for the same thread․
The chart may include additional columns for the Helicoil tap size and pitch, as well as the insert length (usually expressed as a multiple of the thread diameter, such as 1D, 1․5D, or 2D)․ Pay close attention to the units used (inches or millimeters) to avoid errors․ Some charts also provide a decimal equivalent of the fractional drill size for added convenience;
To use the chart, first identify the thread size you need to repair․ Then, locate the corresponding row on the chart․ The drill size listed in that row is the size of the drill bit you should use to prepare the hole before tapping․ Always double-check the chart to ensure you are using the correct drill size for your specific application․
Step-by-Step Guide: Using a Helicoil Tap Drill Chart
Begin by identifying the damaged thread size you intend to repair․ Consult a Helicoil tap drill chart, either in print or PDF format․ Locate the row corresponding to your thread size; this will dictate the correct drill size for preparing the hole․
Next, select the appropriate drill bit according to the chart’s specifications․ Drill out the damaged threads, ensuring the hole is clean and free of debris․ Employ a Helicoil tap, matched to the thread size, to create new threads within the drilled hole․ The chart will specify the correct Helicoil tap to use․
Following tapping, install the Helicoil insert using a dedicated installation tool․ The chart will provide information on the insert length (1D, 1․5D, 2D) to select the appropriate insert․ Break off the tang of the insert․ Verify the repaired thread conforms to the original specifications, ensuring a secure and reliable fit․ This systematic approach, guided by the Helicoil tap drill chart, ensures effective thread restoration․
Selecting the Correct Helicoil Tap and Drill Size
Choosing the right Helicoil tap and drill size is paramount for successful thread repair․ Begin by accurately identifying the original thread size of the damaged component, and then refer to a comprehensive Helicoil tap drill chart, readily available as a PDF for convenient access․
The chart will list the recommended drill size corresponding to your target thread size․ Note that the drill size for a Helicoil insert is larger than the standard tap drill size for the same thread, as it must accommodate the insert itself․
After drilling, select the Helicoil tap specifically designed for use with Helicoil inserts of that thread size․ Confirm the tap matches the insert size you intend to use․ Ensure both the tap and drill are compatible with the material of the workpiece․ Using mismatched sizes can lead to thread damage or insert failure․ Selecting the correct tap and drill, guided by the chart, ensures a strong and lasting thread repair․
Helicoil Installation Process
The Helicoil installation process requires precision․ First, drill out the damaged thread using the drill size specified in the Helicoil tap drill chart for your chosen insert․ Ensure the hole is drilled straight and to the correct depth, accommodating both the insert length and the fastener․
Next, tap the newly drilled hole with the Helicoil tap, ensuring it is aligned correctly․ Apply cutting fluid to aid the tapping process and reduce friction․ Tap to the required depth, maintaining a steady and even pressure․ Remove the tap and clean the tapped hole of any debris․
Insert the Helicoil insert into the installation tool․ Rotate the tool to thread the insert into the tapped hole, continuing until it is properly seated, typically about a quarter to a half turn below the surface․ Finally, use a tang break-off tool to remove the installation tang, leaving the repaired thread ready for use․
Common Mistakes When Using Helicoil Inserts
Several common mistakes can occur when using Helicoil inserts, leading to compromised repairs․ One frequent error is using the incorrect drill size, failing to consult the Helicoil tap drill chart accurately․ This can result in threads that are either too tight or too loose for the insert․
Another mistake is improper tapping, such as tapping at an angle or not tapping deep enough․ Insufficient lubrication during tapping can also damage the threads․ Failing to clean the tapped hole thoroughly before installing the insert is also a common error․
Furthermore, using the wrong installation tool or technique can damage the insert during installation․ Applying excessive force or cross-threading the insert can lead to failure․ Finally, neglecting to break off the tang properly, or breaking it off unevenly, can obstruct the fastener and compromise the repair’s integrity․ Always double-check sizes and follow instructions carefully․
Troubleshooting Helicoil Installation Issues
Encountering issues during Helicoil installation is not uncommon, but most problems can be resolved with careful troubleshooting․ If the insert is difficult to thread into the tapped hole, ensure the hole is clean and properly tapped, consulting the helicoil drill chart․ Check for any debris or obstructions that might be hindering the insert․
If the insert breaks during installation, it could be due to excessive force or cross-threading․ Remove the broken insert and re-tap the hole, ensuring proper alignment․ If the tang breaks off unevenly, use pliers or a specialized tool to carefully remove the remaining piece․
If the installed insert feels loose, verify that the correct tap and drill sizes were used, referencing the appropriate chart․ A loose insert may also indicate that the parent material is too weak․ In such cases, consider using a longer insert or a different repair method․ Ensure compatibility and proper technique․
Where to Find Helicoil Tap Drill Chart PDFs
Locating reliable Helicoil tap drill chart PDFs is crucial for ensuring accurate thread repair and reinforcement․ One of the primary sources is the manufacturer’s website, such as Stanley Engineered Fastening, which often provides comprehensive technical documents for their Helicoil products․ These official charts are typically the most accurate and up-to-date․
Another excellent resource is online industrial supply distributors like Viking Industrial Supply or Mutual Screw & Supply, who often host PDFs of Helicoil charts for customer convenience․ Engineering and machining forums can also be valuable sources, as experienced users frequently share helpful documents and links․
Additionally, websites like Scribd and other document-sharing platforms may contain uploaded Helicoil tap drill charts․ However, exercise caution when using these sources, verifying the chart’s accuracy against official manufacturer data․ Always prioritize charts that specify the ASME B18․29․1 standard for Helicoil tap sizes to ensure compatibility and proper installation․ Confirm the chart’s source before usage․