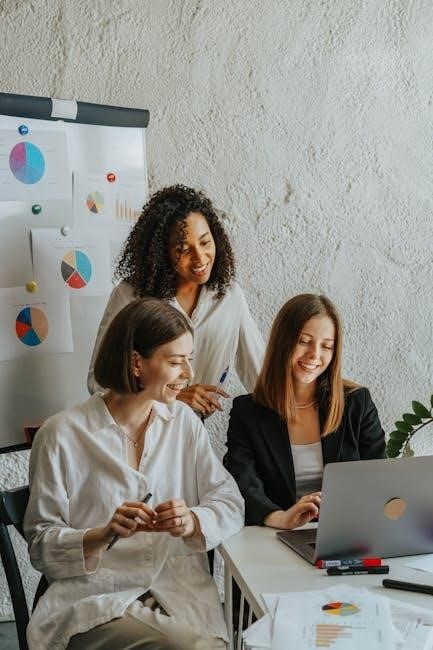
countersunk hole dimensions chart pdf
Countersunk Hole Dimensions: An Overview
Countersunk holes are essential in various applications, requiring precise dimensions for proper functionality. Charts and PDFs provide comprehensive data, offering standardized measurements for diameter, depth, and angle. Utilizing these resources ensures accurate execution and optimal performance in projects.
Understanding Countersunk Holes
Countersunk holes are specifically designed to accommodate fasteners, like flat head screws, allowing them to sit flush with or slightly below the material’s surface. This design enhances aesthetics and prevents protrusions, ensuring a smooth and safe finish. The dimensions of these holes are critical for achieving the desired effect and functionality. Charts and PDFs provide detailed specifications for various screw sizes and standards, ensuring compatibility and proper fit. Understanding these dimensions is essential for engineers, machinists, and DIY enthusiasts alike. Accurate countersinking not only improves the appearance of a project but also contributes to its structural integrity and safety. By consulting reliable dimension charts, users can avoid common errors and achieve professional-quality results. Proper execution is paramount for optimal fastener seating and overall project success.
Purpose of Countersunk Holes
The primary purpose of a countersunk hole is to allow a fastener, typically a flat head screw, to reside flush with or slightly below the surface of the material it secures. This is crucial in applications where a protruding screw head could be hazardous or aesthetically unappealing. Countersinking also prevents damage to objects or individuals that might come into contact with the surface. Furthermore, it reduces the risk of the screw head being sheared off or damaged due to impact or abrasion. Countersunk holes are commonly used in woodworking, metalworking, and various assembly processes where a smooth, unobstructed surface is desired. Achieving the correct dimensions, guided by reliable charts and PDFs, is essential for proper fastener seating and optimal performance. This ensures the screw head sits at the intended depth, providing a secure and visually pleasing finish.
Key Dimensions for Countersunk Holes
Key dimensions include the mounting hole diameter, countersink diameter, countersink depth, and countersink angle. These measurements ensure proper fit and functionality when using countersunk fasteners in various applications.
Mounting Hole Diameter (D1)
The mounting hole diameter, often denoted as D1, is a crucial dimension for countersunk holes. It refers to the diameter of the initial hole drilled into the material before creating the countersink. This diameter must be accurately sized to accommodate the shank of the screw or fastener being used. If the mounting hole is too small, the screw will not pass through easily, potentially causing damage to the material or the fastener itself. Conversely, if the mounting hole is too large, the screw may not seat properly, compromising the integrity of the connection.
Choosing the correct mounting hole diameter ensures a secure and flush fit for the fastener, preventing issues such as stripping or loosening over time. Referencing a countersunk hole dimension chart, particularly in PDF format, is essential for determining the precise D1 value based on the screw size and standard being followed. These charts provide detailed specifications that guarantee compatibility and optimal performance.
Countersink Diameter (D2)
The countersink diameter, designated as D2, represents the diameter of the conical recess created to accommodate the head of the screw or fastener. Accurate sizing of D2 is critical for ensuring that the screw head sits flush with the surface of the material, providing a clean and professional finish. If the countersink diameter is too small, the screw head will protrude above the surface, potentially causing obstructions or safety hazards. Conversely, if D2 is too large, the screw head may sink too deeply, reducing the holding power of the fastener.
To determine the appropriate countersink diameter, consult a comprehensive countersunk hole dimension chart, often available in PDF format. These charts provide precise measurements based on the screw size, head type, and applicable standards. Following these guidelines ensures optimal functionality and aesthetic appeal. Incorrect D2 dimensions can lead to compromised structural integrity and an unprofessional appearance.
Countersink Depth
Countersink depth is a critical dimension that dictates how far the countersink extends into the material. This depth ensures the screw head sits flush or slightly below the surface, preventing protrusion and interference. Accurate depth is crucial for achieving a smooth, professional finish and maintaining structural integrity. If the depth is insufficient, the screw head will remain above the surface, compromising aesthetics and potentially causing safety issues. Conversely, excessive depth weakens the material and reduces the screw’s holding power.
To determine the appropriate countersink depth, refer to dimension charts, often available in PDF format. These charts correlate screw size and head type with recommended depth values. Factors influencing depth include material thickness and desired flushness. Proper depth ensures optimal screw seating and load distribution. Deviations from recommended depths can lead to functional problems and aesthetic imperfections.
Countersink Angle
The countersink angle is a crucial parameter defining the conical shape of the countersink, typically measured in degrees. This angle must match the angle of the screw head to ensure a proper fit. Common angles include 82°, 90°, and 120°, each designed for specific screw types. An incorrect angle will prevent the screw head from seating correctly, leading to instability and potential damage.
Dimension charts, often found in PDF format, provide angle specifications for various screw sizes and standards. These charts are essential for selecting the correct countersink tool and achieving a flush, secure connection. The angle is directly related to the screw head’s geometry, ensuring even load distribution and preventing stress concentrations. Deviations from the specified angle can compromise the integrity of the joint and reduce its overall strength. Therefore, precise angle selection is paramount for reliable performance.
Countersunk Hole Dimension Charts
Countersunk hole dimension charts are indispensable tools for engineers, machinists, and hobbyists alike. These charts, often available in PDF format, provide precise measurements for creating countersunk holes that perfectly accommodate flat-head screws and other fasteners. A typical chart includes critical dimensions such as the mounting hole diameter, countersink diameter, countersink depth, and countersink angle. These parameters ensure that the screw head sits flush with the surface, providing a clean and professional finish.
The charts are organized by screw size and standard, making it easy to find the correct dimensions for a specific application. ANSI and ISO standards are commonly referenced, providing standardized measurements for consistent results. Detailed charts also consider material type and screw head type, offering specific recommendations for optimal performance. Properly utilizing these charts minimizes errors, improves the quality of the finished product, and ensures structural integrity.
ANSI Metric Countersunk Hole Dimensions
ANSI metric countersunk hole dimensions are critical for ensuring proper fit and function in various mechanical applications. These dimensions, standardized by the American National Standards Institute (ANSI), provide precise measurements for countersunk holes designed to accommodate metric flat head screws. The ANSI metric standard dictates the mounting hole diameter, countersink diameter, countersink depth, and countersink angle, ensuring that the screw head sits flush with the surface of the material.
Charts detailing these dimensions are essential for engineers, machinists, and manufacturers to achieve accurate and consistent results. These charts typically list screw sizes, corresponding pilot hole diameters, and countersink specifications, allowing for easy reference and application. Following ANSI metric standards ensures interchangeability and compatibility of components, streamlining assembly processes and enhancing overall product quality. Utilizing these standards helps maintain structural integrity and a professional finish.
Inch Countersunk Hole Dimensions
Inch countersunk hole dimensions are crucial for projects utilizing imperial measurements; These dimensions specify the precise measurements required to create countersunk holes that accommodate flat head screws designed to sit flush with a surface. Key dimensions include the mounting hole diameter, countersink diameter, countersink depth, and countersink angle.
Detailed charts and tables provide these specifications, categorized by screw size, ensuring accurate execution. These resources are indispensable for machinists, engineers, and hobbyists alike, guaranteeing proper screw seating and preventing protrusions. Accurate inch countersunk hole dimensions contribute to both the aesthetic appeal and functional integrity of the final product. Proper adherence to these dimensions ensures that fasteners do not interfere with mating parts or pose safety hazards. These charts facilitate consistent and reliable results. By adhering to these standards, projects achieve a professional finish.
Factors Affecting Countersunk Hole Dimensions
Several key factors influence the selection and application of countersunk hole dimensions. These factors ensure proper fit and functionality of the fastener within the countersunk hole. Material type and thickness play a crucial role, as harder materials may require different dimensions compared to softer ones. The screw head type, whether it’s a flat head, oval head, or other, dictates the countersink angle and diameter.
Standards also impact dimensions, adhering to ISO, DIN, or ANSI guidelines ensures compatibility and consistency. The desired aesthetic finish, whether a flush or slightly recessed fit, affects the depth of the countersink. The application’s load requirements also influence dimensions, as higher stress applications may require larger or deeper countersinks. Considering these factors is essential for selecting the appropriate dimensions. This ensures optimal performance and longevity of the assembly. Ignoring these factors can lead to improper seating, reduced strength, or even failure of the joint.
Material Type and Thickness
The material type and thickness significantly influence countersunk hole dimensions. Different materials possess varying hardness and machinability, impacting the countersinking process. Softer materials like aluminum require different dimensions and techniques compared to harder materials like steel. The material’s thickness determines the depth of the countersink; thicker materials may necessitate deeper countersinks to accommodate the screw head properly.
When working with thinner materials, care must be taken to avoid excessive countersinking, which can weaken the structure. Thicker materials can withstand deeper countersinks without compromising structural integrity. Material properties like elasticity and plasticity affect the countersink’s shape and size. Heat treatment can also affect the material’s properties, thereby influencing the required countersink dimensions. Always consult material-specific guidelines and charts to determine appropriate dimensions for different materials and thicknesses. Proper consideration ensures a secure and flush fit for fasteners. Ignoring these can result in issues like stripping threads, material deformation, and compromised joint strength.
Screw Head Type
The screw head type is a crucial factor when determining countersunk hole dimensions. Different screw heads necessitate specific countersink angles and diameters to achieve a flush fit. Flat head screws, for instance, require countersinks with matching angles to ensure the head sits perfectly flush with the surface. Button head screws, on the other hand, may need shallower countersinks due to their rounded profile.
Oval head screws often require a combination of countersinking and counterboring to accommodate both the tapered head and the cylindrical base. Pan head screws typically do not need countersinking, as they are designed to sit above the surface. The screw head’s diameter dictates the required countersink diameter; a larger head needs a wider countersink. The head angle determines the countersink angle; common angles include 82 degrees and 90 degrees. Always refer to screw head specifications and dimension charts to select appropriate countersink dimensions. Failure to match the countersink to the screw head can lead to protrusion, reduced strength, or aesthetic issues.
Standards for Countersunk Holes
Adhering to established standards for countersunk holes is paramount for ensuring compatibility and consistent performance across various applications. Standards organizations like ANSI, ISO, and DIN provide detailed specifications for countersunk hole dimensions, including diameters, depths, and angles. These standards consider different screw head types, materials, and tolerance requirements. Utilizing standard dimensions facilitates interchangeability of fasteners and simplifies design processes.
ISO standards, for example, outline specific requirements for metric countersunk holes, while ANSI standards cover inch-based dimensions. DIN standards offer additional specifications, particularly common in European engineering practices. These standards often include charts and tables that provide precise dimensions for various screw sizes and head types. Following these standards ensures that countersunk holes are accurately created, leading to secure and aesthetically pleasing assemblies. Deviations from these standards can result in improper seating, reduced structural integrity, and potential safety hazards. Consulting relevant standards documents and dimension charts is crucial for achieving reliable and consistent results in manufacturing and engineering projects.
ISO Standards
ISO standards provide internationally recognized specifications for countersunk holes, ensuring uniformity and interchangeability in engineering and manufacturing practices. These standards define precise dimensions for various metric screw sizes, including mounting hole diameters, countersink diameters, depths, and angles. ISO standards consider different tolerance classes and material properties, offering detailed guidelines for achieving optimal fit and performance.
Referencing ISO standards is crucial for designers and manufacturers aiming to create components that comply with global requirements. These standards often include comprehensive charts and tables that outline specific dimensions for different screw types, such as flat head screws and socket head cap screws. The charts provide a clear reference for selecting the appropriate countersunk hole dimensions based on the chosen fastener. Adhering to ISO standards ensures that the countersunk holes are accurately machined, resulting in secure and aesthetically pleasing assemblies. Compliance with ISO standards also facilitates international trade and collaboration by promoting consistency and compatibility across different regions.
DIN Standards
DIN standards, originating from Deutsches Institut für Normung, offer specific guidelines for countersunk hole dimensions, crucial for precise engineering applications. These standards provide detailed specifications for various metric screw sizes, covering mounting hole diameters, countersink diameters, depths, and angles. DIN standards ensure consistent and reliable results in manufacturing processes.
DIN standards also consider factors such as material type and screw head type, providing comprehensive charts and tables for accurate dimensioning. For example, DIN 7991 specifies requirements for hexagon socket countersunk head cap screws, including dimensions for head diameter, countersink angle, and thread specifications. These standards are essential for engineers and manufacturers who need to adhere to German industrial norms. Compliance with DIN standards ensures proper seating of screws and optimal functionality of assembled components. Utilizing DIN standards promotes interchangeability and compatibility, leading to efficient and cost-effective production processes. By following these guidelines, manufacturers can achieve high-quality and reliable countersunk hole designs;
Applications of Countersunk Holes
Countersunk holes find extensive applications across various industries due to their ability to create flush surfaces. In woodworking, they allow screws to be recessed, preventing snagging and providing a clean finish. Similarly, in metalworking, countersunk holes are crucial for ensuring smooth surfaces on machine guards and covers. Aerospace engineering utilizes countersunk holes in wing panel and fuselage assembly, maintaining aerodynamic integrity.
Electronics manufacturing benefits from countersunk holes for secure and flush mounting of components on circuit boards. Automotive applications include interior trim and exterior body panels, where flush fasteners enhance aesthetics and safety. Furniture construction relies on countersunk holes for a seamless and professional appearance. In summary, countersunk holes are essential in any application requiring a smooth, unobtrusive fastening solution. Their versatility and functional benefits make them indispensable in numerous manufacturing and construction processes, ensuring both aesthetic appeal and structural integrity.